Novel approaches to next-generation product solutions incorporating improved functionality such as higher strength, ductility, durability, and material resilience.
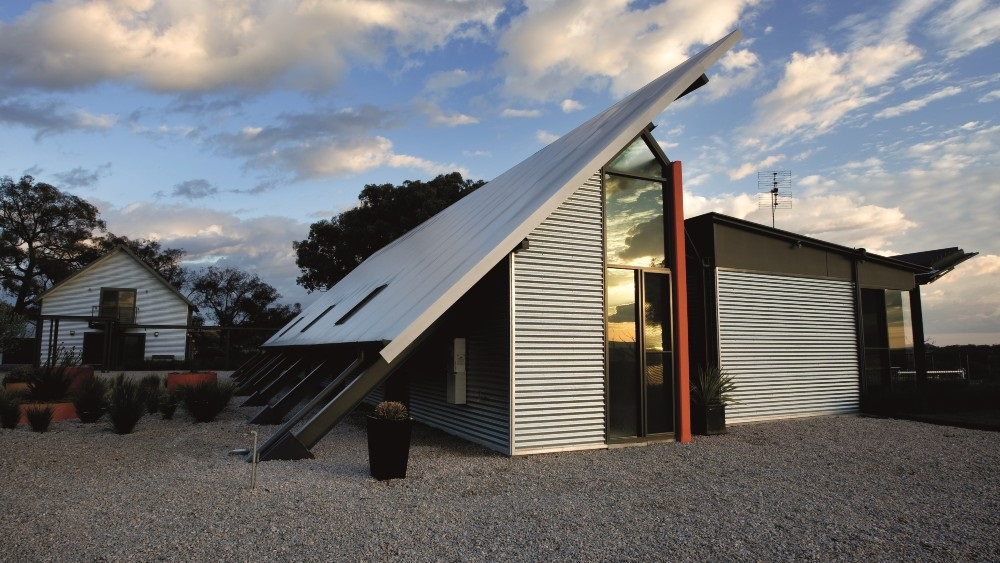
Novel approaches to next-generation product solutions incorporating improved functionality such as higher strength, ductility, durability, and material resilience.
Academic: Irene Yarovsky (RMIT)
Industry: Mark Eckermann (BlueScope) Bradley Taylor (Infrabuild)
This research program brings together multi-disciplinary teams to investigate the fundamental mechanisms that underpin potential steel developments in order to commercially address new opportunities created by innovation in new market segments for flat and long steel products. A range of complementary core research activities and enabling technologies skills will be supported, from computational molecular dynamics, advanced synthesis chemistry, cutting-edge analytical equipment, through to experimental and numerical analysis of structures.
New fundamental and applied understanding will be generated which underpins the development of new generation, high value-added product innovations, mainly for Australian residential and commercial buildings, infrastructure, wire and other product applications. The challenge and the intended outcome is to produce these new products with minimal production cost escalations or capital investment.
Program 2 is comprised of two sub-programs:
- Product Durability & Functionalisation
- Structural & Cold-Formed Steel Optimisation
Research within this project, performed by The Royal Melbourne Institute of Technology (RMIT) and BlueScope Steel (BSL), will use molecular simulation methods to better understand the structure and behaviour of certain coating systems both in solution and in association with other materials. This is in partnership with chemical analysis work that interrogates the properties of interest. The knowledge generated in this work will assist in the development of these materials for potential coating applications.
Team: Professor Irene Yarovsky (RMIT), Ben McLean (RMIT), Shane MacLaughlin (BlueScope), Josh Brooks (BlueScope), Monika Wyszomirsk (BlueScope), Macquire Bryant (BlueScope), Ari Yazidi (BlueScope)
This project brings together Deakin University, Infrabuild Wire and InfraBuild Manufacturing to deliver advancements across both wire and reinforcing products.
This project is aimed at improving the life of hot dip coated wire. The team will deliver process and material innovations to InfraBuild Wire’s hot dipped coated steel wire products, targeting greatly enhanced durability in a variety of conditions.
An initial strategy to improve corrosion resistance, while maintaining sufficient ductility, will focus on optimal levels of additions and thermal processing. Outcomes from the research into these new alloys and processes will allow near-term commercial adoption. Next generation, environmentally friendly protective coating formulations will also be designed and developed, with a longer-term view towards commercial adoption.
Team: Dr Anthony Somers (Deakin), Mohsen Saeedikhanigeraei (Deakin), Bradley Taylor (Infrabuild Wire), Malcolm Robertson (Infrabuild Wire), Dr Lauren Andrews (Infrabuild Wire), Dr Robert Fabien (Infrabuild Wire), Associate Professor Daniel Fabijanic (Deakin)
A collaboration between Deakin University, Infrabuild Wire and InfraBuild Manufacturing, this project will investigate process improvements that induce optimal strength-ductility balance in reinforcing construction steel products.
After developing and understanding these property relationships, the team will design alloys to maximise the product performance and conduct up-scaling industrial trials within InfraBuild Manufacturing. The product advancements will provide the construction industry with greater performance and reliability.
Team: Associate Professor Daniel Fabijanic (Deakin), Jithin Joseph (Deakin), Dr Robert Fabien (Infrabuild Wire), Graeme McGregor (Infrabuild Wire), Anthony Ng (Infrabuild Wire), Greg Morris (Infrabuild Wire), Sharmy Francis (Infrabuild Wire), Bradley Taylor (Infrabuild Wire), Dr Anthony Somers (Deakin)
The University of Wollongong (UOW) and Bisalloy Steels have developed a project which focuses on the additive manufacturing of welded overlay. The project will investigate and trial automated/ robotic wire arc additive manufacturing to fabricate welded hard-facing overlay on Quenched and Tempered (Q&T) steels.
Bisalloy Steels is Australia's only manufacturer of high-tensile, abrasion-resistant Q&T steel plates used for armour, structural, and wear-resistant steel applications. Through experimental design and trials, the team will develop an optimised methodology for high hardness (wear) and toughness (impact, blast) of welded overlay which has significantly improved performance.
It will then focus on the development of an automated hard-facing solution for which a robot operator can easily program and does not require a high level of welding skill and knowledge.
Team: Professor Huijun Li (UOW), Dr Dake Yu (Bisalloy), Dr Willy Pang (Bisalloy), Emeritus Professor John Norrish (UOW), Associate Professor Zengxi (Stephan) Pan (UOW), PhD candidate Durga Tandon (UOW)
This is a PhD-based project between BlueScope Limited (BSL) and the University of Wollongong (UOW), which focuses on the development of fundamental understanding and processing schedules for hot rolled microalloyed steels with 800MPa strength.
The future development of BSL’s hot rolled strip steels portfolio requires incorporation of more advanced high strength steels in order to be internationally competitive and contest supply for domestic users of these products. Importantly, such developments should be aligned to the capabilities of BSL’s Hot Strip Mill (HSM).
The critical requirements for this project are a cost-effective approach to alloying elements, a good combination of strength and toughness, metallic coating or painting capability, and weldability. For BSL, the anticipated outcome of this research will be the development of micro-alloyed, hot-rolled steel strip with 800 MPa strength, which can be produced within the HSM’s capability.
Team: Professor Elena Pereloma (UOW), Chris Killmore (BlueScope), Mark Eckermann (BlueScope), Lauren Smee (BlueScope), Dr Paton Wilson (BlueScope), PhD candidate Gholam Baqeri (UOW)
This project between UOW and BSL, provides a contemporary view on the latest generation of polymer chemistries used to formulate radiation cured coatings and technical insights regarding the formulation of radiation cured coatings in applications requiring high outdoor durability.
Team: Dr Paul Zulli (UOW), Andrew Lang (UOW), Jason Hodges (BlueScope), Jim Viatos (BlueScope), Greg Foster (BSL)
This project between University of Wollongong (UOW) and Liberty Primary Steel (LPS) will focus on the production of 425+ MPa thick rolled sections at Liberty Primary Steel Rolling Mills.
Steel sections of strength greater than 400 MPa are becoming more widely used in lattice-style transmission line engineering due to weight considerations and high loading capacity, as are larger angle sections. Savings in weight (~8%) and cost (~9%) could be achieved with transition to 300mm large angle steel of 420 MPa yield strength in traditional power transmission towers.
The expected outcome of the project is the development of a commercially viable microalloyed steel with greater than 425 MPa yield strength for large angle production within the process capabilities of LPS’s Steelmaking Plant and Rolling Mills.
Team: Chief Investigator Professor Elena Pereloma (UOW), Yue Zhao (UOW), Amir Baghdadi (UOW), Mark Bubicich (Liberty), Paul Fitzpatrick (Liberty)
This project brings together expertise from the University of Wollongong (UOW) and BlueScope (BSL), and focuses on the development, analysis and design of cold-formed steel (CFS) products for mid-rise apartment building frames.
From Project B2.1 of the first ARC Steel Research Hub, it was evident from a conceptual design perspective that the lateral load demand for the lower storeys of an archetype CFS intensive mid-rise apartment building in Australia is beyond the capacity of existing CFS shear panels.
In this new expanded project, novel, high-capacity shear panels will be designed for several load levels using highly efficient steel products already used in the construction of CFS mid-rise apartment buildings.
Team: Professor Lip Teh (UOW), Dr Jungho Dong (UOW), Trevor Clayton (BlueScope), Mark Eckermann (BlueScope), Paul Jones (BlueScope), Glen Hampton (BlueScope), Ben Zietsch (BlueScope) Dr Aziz Ahmed (UOW), PhD candidate Subham Dharel (UOW)
A joint venture between the University of Wollongong (UOW) and BlueScope Limited (BSL), this project was derived, in part, from research directions undertaken in a previous project under Hub I entitled “Innovative cladding and ventilation solutions for mid-rise residential buildings”.
This new project aims to provide rigorous, evidence-based information to guide the optimal application of steel building products, to both current and future Australian climatic conditions and to improve building regulations.
The project involves a set of seven sub-projects, each focused on a specific aspect of a building’s thermal and moisture-management performance. The team is focused on developing mathematical models and experiments to further the understanding of the building physics related to certain construction assemblies.
Team: Dr Alan Green (UOW), Associate Professor Georgios Kokogiannakis (UOW), Dr Steve Beltrame (UOW), Jamie Adams (BlueScope), Mark Eckermann (BlueScope), Glen Hampton (BlueScope), Jack Whitford (BlueScope), Dr Leela Kempton (UOW), Professor Paul Cooper (UOW)
This project will be led by the University of Sydney (USyd), together with BlueScope Limited (BSL), to better understand the way in which floor joists are manufactured.
The project will investigate specific issues with steel floor joists manufactured in the wall frame orientation and will determine design methodologies for typical dead and live loads.
The research will investigate the issues with steel floor joists manufactured in the wall frame orientation to understand serviceability criteria to minimise vibration, deflection and noise in the floor systems and design criteria to minimise noise and floor vibration will be developed. The initial focus is on determining the span capabilities of the ENDUROFRAME floor system, which uses unlipped chords, with additional investigations to determine the impact of lipped chords.
Team: Associate Professor Cao Hung Pham (USyd), Paul Jones (Enduroframe, BlueScope), Mark Ekermann (BlueScope), Trever Clayton (BlueScope), PhD Candidates Hoang Vu Le (USyd)and Ruilun Zhang (USyd)
This project brings together the National Association of Steel-Framed Housing Inc (NASH), the University of Wollongong (UOW) and the team at Sustainable Building Research Centre (SBRC) to investigate the thermal performance of steel-framed ceilings.
This research will provide valuable scientific input into upcoming proposed amendments to Energy Efficiency provisions for Residential Buildings (Houses and Apartments) in the National Construction Code 2022 revision.
Team: Dr Alan Green (UOW), Georgios Kokogiannakis (UOW), Mike Kelly (NASH), Mark Eckermann (BlueScope), Ken Watson (NASH), Professor Paul Cooper (UOW), Dr Steve Beltrame (UOW)
Header image credit: COLORBOND® Ultra steel in the colour Surfmist® and COLORBOND® Coolmax® steel in the colour Whitehaven®
Sustainability Building Research Centre, New South Wales